Although the servo output of an RC receiver provides all the information required to control an L298N motor driver, the signal must be evaluated and recoded in a suitable manner, as the control logic of the motor driver is fundamentally different to that of an RC servo.
This task can be performed by the RCRX2Bridge module. This is a single-chip solution that evaluates one channel at a time and thus controls one motor of the L296 bridge. The circuit is very simple, and the module is quick to assemble with the breakout board.
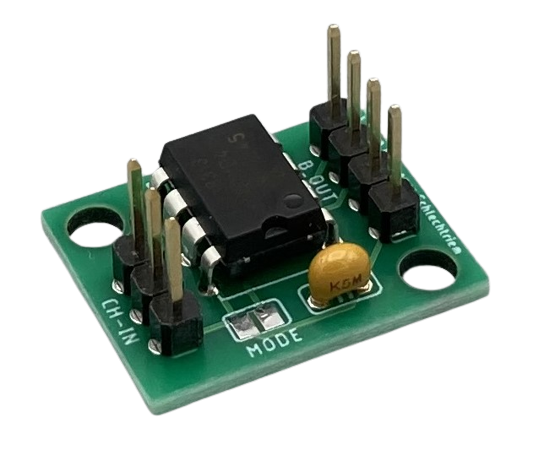
RCRX2Bridge supports the two common, but different control modes of L298N bridges: Models with 2/4 phases and models with two logic inputs and one speed input.
Control of bridges with two inputs
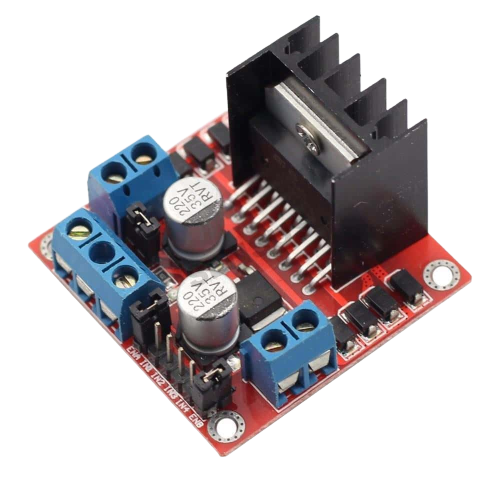
The RCRX2Bridge module is connected to the receiver on the input side, as shown in the picture. The input pins of the motor driver IN1 and IN2 are connected to the output pins of the breakout board as shown in the picture. If a second motor is to be controlled, a second RCRX2Bridge module is required.
Control of bridges with three inputs
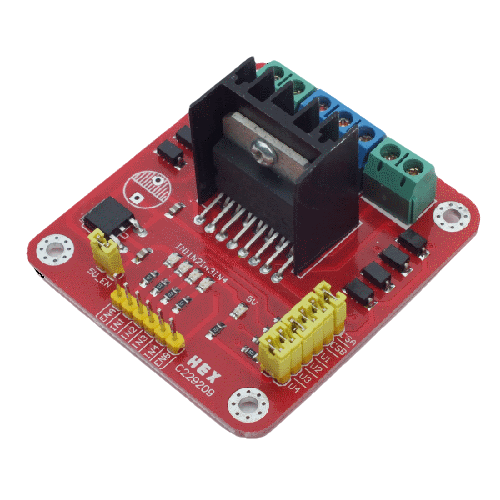
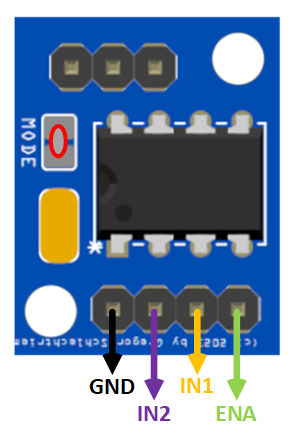
For this application, the RCRX2Bridge module is configured for the changed logic using a solder bridge at “MODE” and then also connected to the receiver on the input side in this case, as shown in the article image.
The input pins of the motor driver ENA, IN1 and IN2 are connected to the output pins of the breakout board as shown in the picture. If a second motor is to be controlled, a second RCRX2Bridge module is also required here.
The kit for the breakout board with the RCRX2Bridge controller is available in the store.